Your challenges. Our Expertise.
We believe that it is the one who best understands the end users that will create the best products and services for them. At Semcon, we combine engineering expertise, digital services and sustainability know-how in a unique offering for product, production and service development.
Let´s build you the perfect tech team
The perfect solution requires the perfect set-up. And with an expert tech team from Semcon, achieving your dream results is child's play. Welcome to our wonderful world of innovation!
Learn more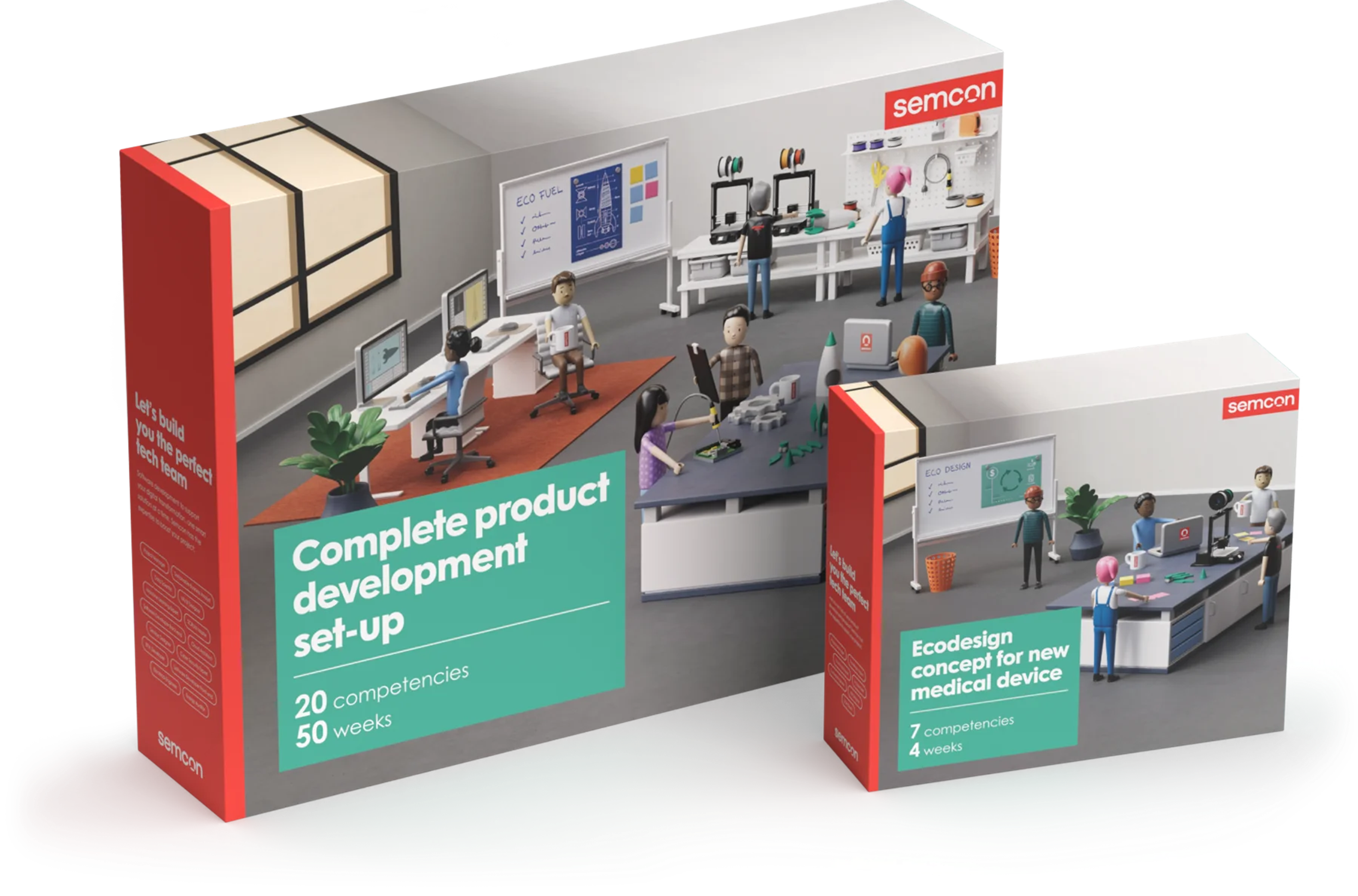
We add new perspectives to your business
To develop technology that improves people’s lives while respecting our planetary boundaries and protecting human rights is a task that is far from simple. It requires both the courage to question and try new things, and humility in the face of the fact that there is always more to learn.
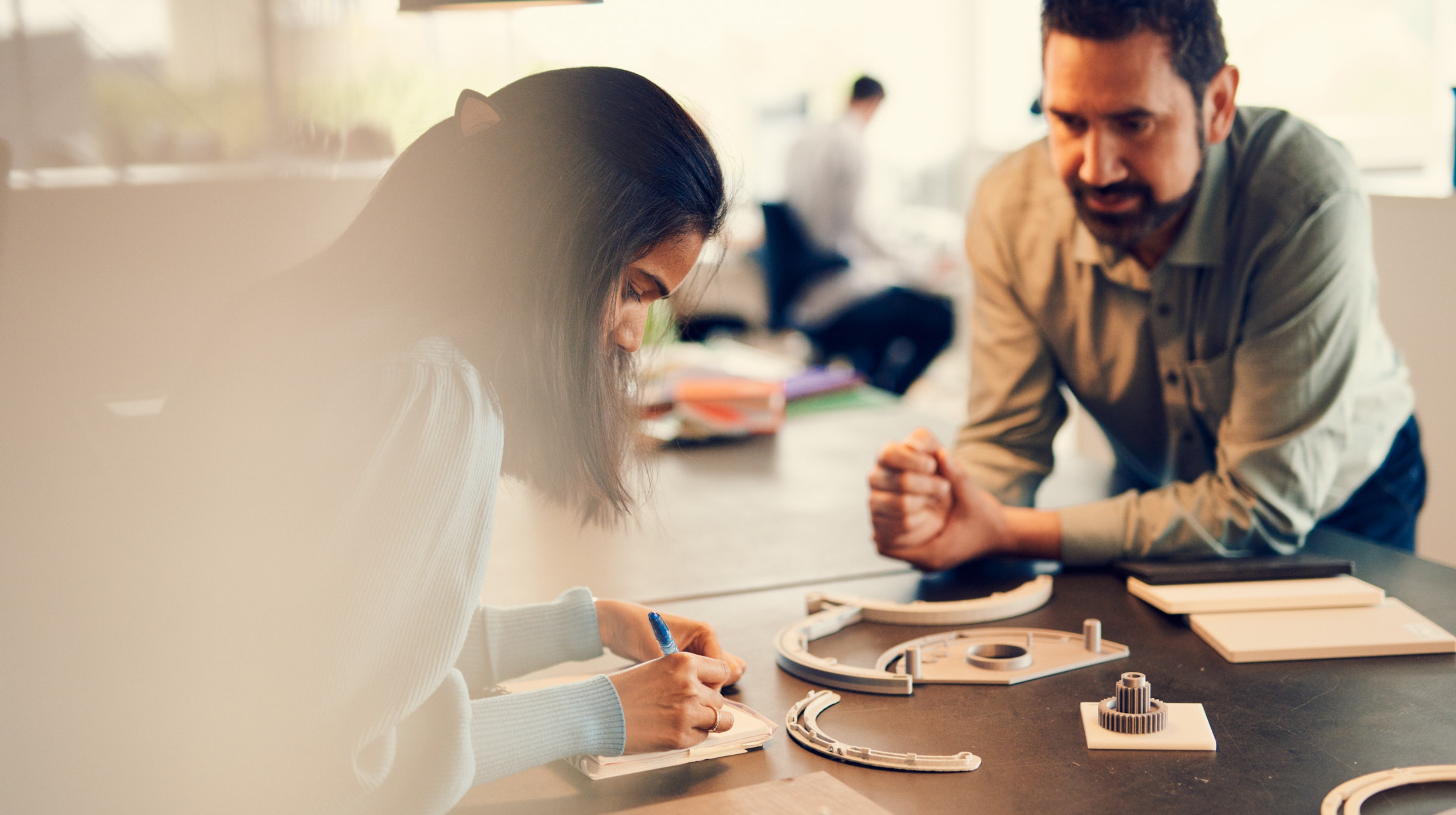
Unique combination of strenghts
Semcon has approximately 1,600 dedicated experts specialised in their respective fields. Together, we have the breadth to be able to support your business throughout the journey. And the edge to push you a little further. From the very first idea to the finished solution and beyond. Because a sustainable business model requires us to think all the way through and look at all steps in the life cycle.
Watch video showcasing some of our projectsFlexible delivery models
Different needs require different solutions. We offer different kinds of delivery models to find the best match for each customer situation.
A dedicated team of experts
Get ahead by accessing the full range of our expertise. For 40 years we have fine-tuned our processes, tools and methods to help you take the next technological leap.
Get in touch
Let's talk about how we can create something great together. Find the contact info to your local Semcon office.
Strategic Business Design
In this era of constant change, a web of powerful megatrends forces us all to reconsider our society and embrace fresh approaches and new perspectives. Human needs, behaviours, and motivations evolve rapidly, while digitalisation disrupts every sector. To confront our planetary crisis, we must transition from a fossil-fuel-driven linear society to a net-zero circular one.
Read moreProduct Development
The journey towards a finished product is filled with challenges and demands to consider. Every day, we at Semcon help our customers to turn their ideas to reality. Creating innovative, sustainable products and solutions with the help of new technologies. Our experience from all segments, comprehensive expertise and focus on research, make Semcon a long-term development partner to our customers.
Read moreDigital Solutions
In our rapidly changing and increasingly complex world, we must be quick and agile in how we adapt our business models, companies and entire communities to a new digital and more sustainable reality. Not next week. Not tomorrow. But today.
Read moreProduction Development
Many companies face significant changes in their production environment. To mobilise for the future, it is important to take advantage of the opportunities offered by, for example, digitalisation and automation. This may lead to a more sustainable production, efficiency improvements, safer work environment or new business models.
Read moreProject Excellence
Do you have projects that do not produce the expected effect? At a time when most businesses are undergoing rapid change, it is important to do the right things and to do things right. At Semcon, we help our customers every day to develop and streamline their project operations. We provide support throughout the entire journey – from preliminary study to the desired result.
Read moreSustainable Business
Developing technology that improves people’s lives while respecting our planetary boundaries and protecting human rights. The task is far from simple. It requires both the courage to question and try new things, and humility in the face of the fact that there is always more to learn.
Read moreQuality Excellence
Can you afford not to do the right thing? In a world that is changing faster than ever, managing requirements and directives is becoming quite a challenge for many organisations. If you don't keep up, it can be expensive and exhausting to recover. But how do you know where to start?
Read moreProduct Information
During 2023 Semcon's business area Product Information branched out as the independent brand Aleido. Their aim is to ensure your advanced product and solutions are always simply understood by the countless people who depend on them. For more information visit aleido.com.
Read more