Case
Pilot project speeds up healthcare innovation
Healthcare systems and medical staff are expected to be able to deliver better care to more people. The care should also maintain a high level of quality, be safe and cost less. To help deliver better medtech products more quickly, Mölnlycke Health Care wanted to test a new way of working with Semcon.
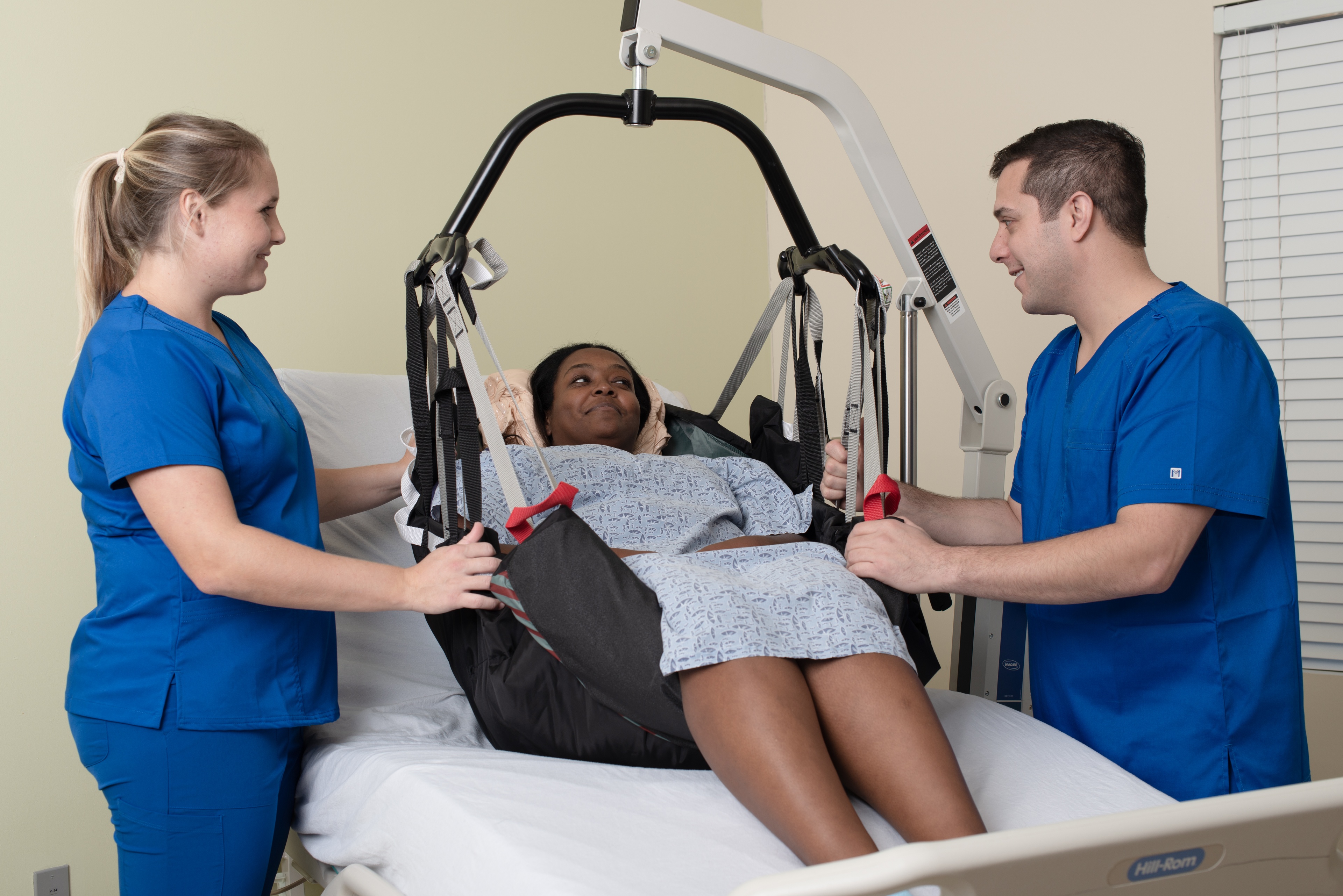
CustomerMölnlycke Healthcare
IndustryLife Science
CompetencesProduct DevelopmentProject ManagementQuality AssuranceValidationDesign & User Experience
Background
Mölnlycke is a world-leading supplier of medical technology solutions. The company’s goal is to improve healthcare outcomes around the world, and to succeed at that, Mölnlycke places great focus on innovation and dialogue with its customers. The company is therefore committed to finding new ways of working that enable them to more quickly meet their customers’ requests and the patients’ needs.
New solutions for effective product development
Semcon and Mölnlycke have enjoyed long-term and close collaboration for many years, with Semcon quickly assisting Mölnlycke with specific expertise in various parts of the company. A large part of this work has dealt with documentation, which is extensive within the medtech field due to the strict regulations that each product must follow. When Mölnlycke further developed their product Tortoise, which is a lifting aid for moving and turning patients and thereby preventing pressure ulcers, the company wanted to test a new way of working.
“Because our focus is on our customers, who are accustomed to us meeting their requests for new and better solutions at an ever-increasing pace, we wanted to streamline product development. We have succeeded in this together with Semcon and welcome this changed way of working to free up internal hours for, among other things, more in-depth customer insights,” says Anna Ramström, Global Project Manager at Mölnlycke Health Care.
Full speed ahead
Mölnlycke wanted to test out giving the entire responsibility for verifying the concept for the newly developed product to Semcon. This is resource-intensive work that includes verification and design-output with specifications. Outsourcing the work to Semcon enabled Mölnlycke to move forward with designing new concepts and putting their resources where they will do the most good: in the innovation of new medical technology solutions. Like Tortoise, for example, which resulted from Mölnlycke’s product development and prevents pressure ulcers through air cushions, which in turn distribute the pressure on the patient and facilitate positioning and repositioning. The new product, Tortoise Sling, also makes it easer for healthcare staff to move patients between different beds.
Several of us from Semcon were involved in the project, which means that there is support and expertise to lean on when needed.
Matilda Foung, a Quality Management consultant at Semcon, worked as Design Owner at Mölnlycke for four years. In her role, Matilda was responsible for all technical documentation about a product, which also included requirement specifications, risk analyses and biological evaluations. During the further development of Tortoise, she had the responsibility for the verification of the concept and led the work with the quality department from Semcon’s side. Because the verification of a new medtech product is a sizeable job, a working group was formed with several specialists from Semcon.
“Working with Mölnlycke in this project has been both challenging and really fun. The pace is fast, there’s a lot happening, and the company is constantly looking ahead. Several of us from Semcon were involved in the project, which means that there is support and expertise to lean on when needed,” says Matilda Foung.
Semcon also got the assignment to design Tortoise Sling
In addition to verification, Semcon was also asked to make design drawings of the new product. The work was done by Semcon Studios, where about 90 people with different skill sets work and can be quickly brought in to help solve the customers’ challenges. The work with Tortoise Sling involved drawing the different parts of the product in a CAT tool and then putting them together digitally. This enables risks and problems to be detected and addressed early on.
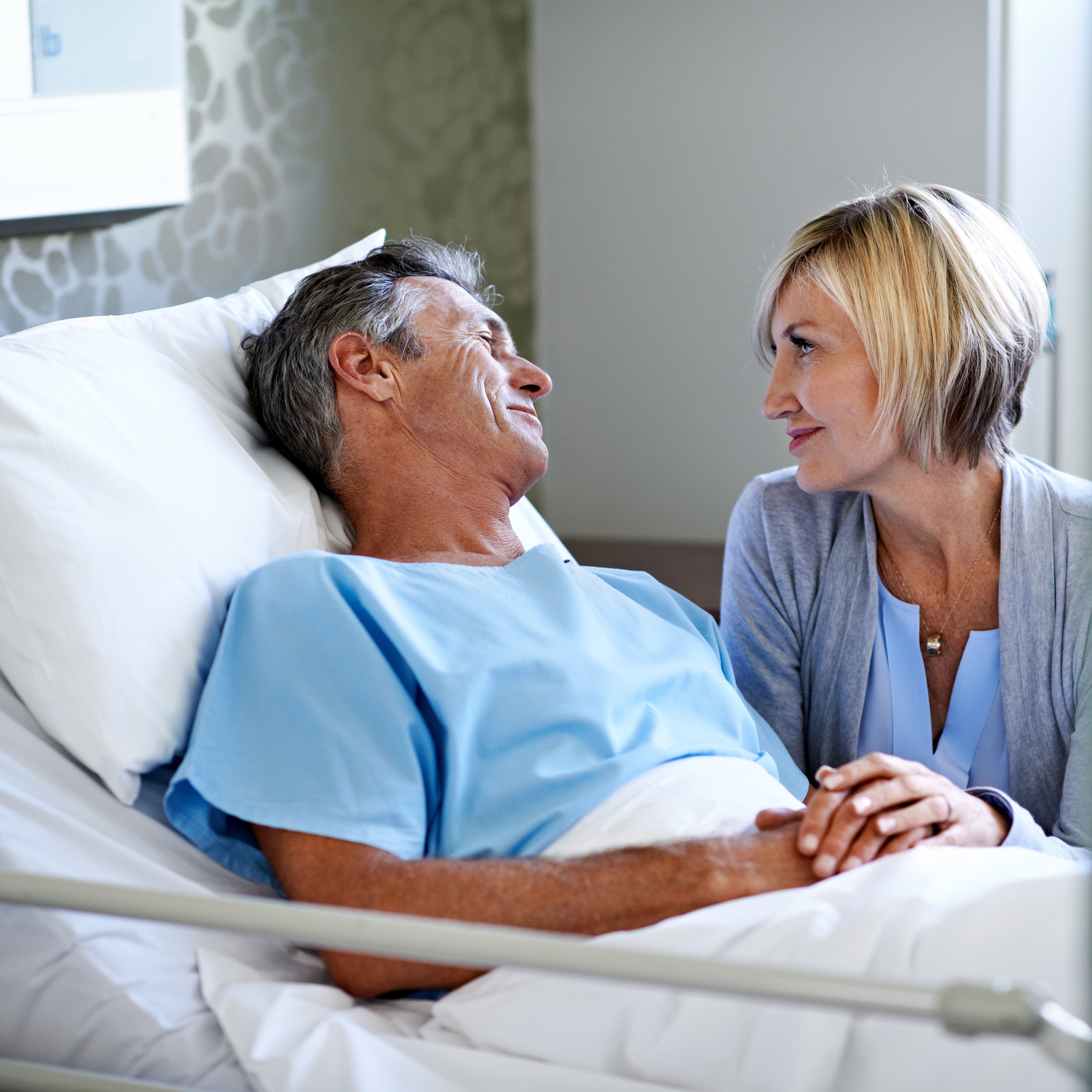
“We received Mölnlycke’s concept and then started working to design it. To avoid obstacles and problems, Semcon joined the project team and its weekly coordination meetings, where concerns and risks could be raised at an early stage. This helped the work to flow without serious obstacles. A big part of the work with Tortoise has been about ensuring that everything works as it should and securing future production,” says Björn Eklund, Area Manager at Semcon.
Semcon is supporting Mölnlycke with these areas of expertise:
Verification
Validation
Design in CAD
Design Control
Rules and Standards
Quality Assurance
Project Management
Product Development
Technical Documentation