Case
New electric motor for milk tankers reduces emissions
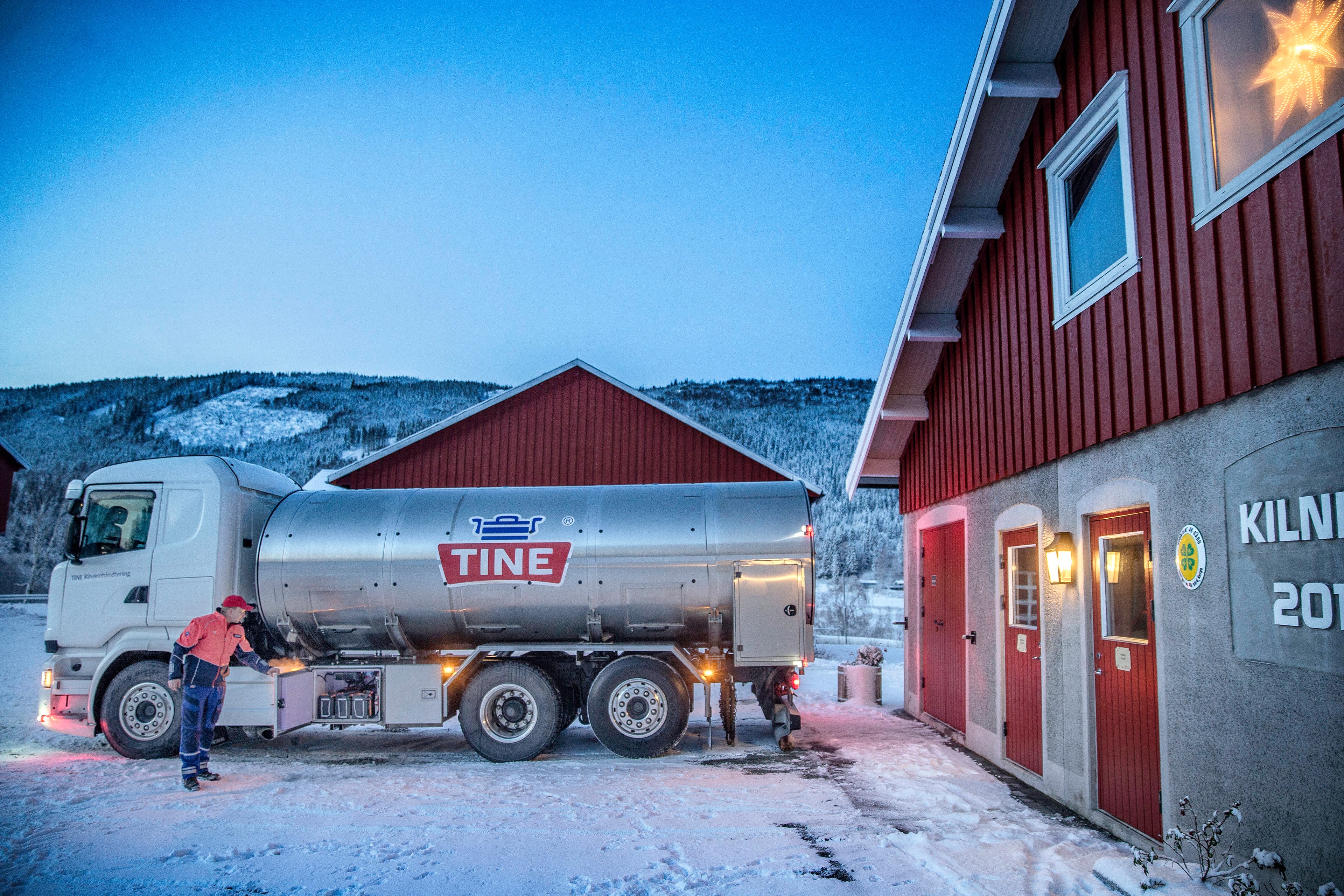
CustomerTine
IndustryLife Science
CompetencesElectrification
Background
Lots of carbon dioxide is emitted unnecessarily every time tankers arrive at farms to collect milk. This is because the trucks use their oversized diesel engines to drive the pump that fills the tank. Technology company Semcon has now developed an electrical system for the milk pump that will reduce diesel consumption for a single truck by up to 5000 litres per year. Noise and emissions at farms will also be reduced. Every tanker pumps milk for about 1000 hours per year, which costs dairies a lot of money. Installing a battery-powered electric motor reduces both the amount of diesel used and wear and tear on the diesel engine.
Tine, a Norwegian company responsible for most transportation of milk in Norway, is planning to install the new pumps in all 250 of its vehicles.
We will reduce our diesel consumption by 1.25 million litres per year when all our milk pumps in Norway run on electricity. This means that CO2 emissions will be reduced by 3200 tonnes a year. This investment in our climate will pay off financially as well. Our costs will be reduced by several million kroner.
– Frode Eggan at Norwegian dairy Tine
More than 120 million litres of diesel a year could be saved if all EU dairies were to adopt this solution. Moreover, the technology can be transferred to other areas as well.
Semcon, Tine and Enova are working in partnership on this project.
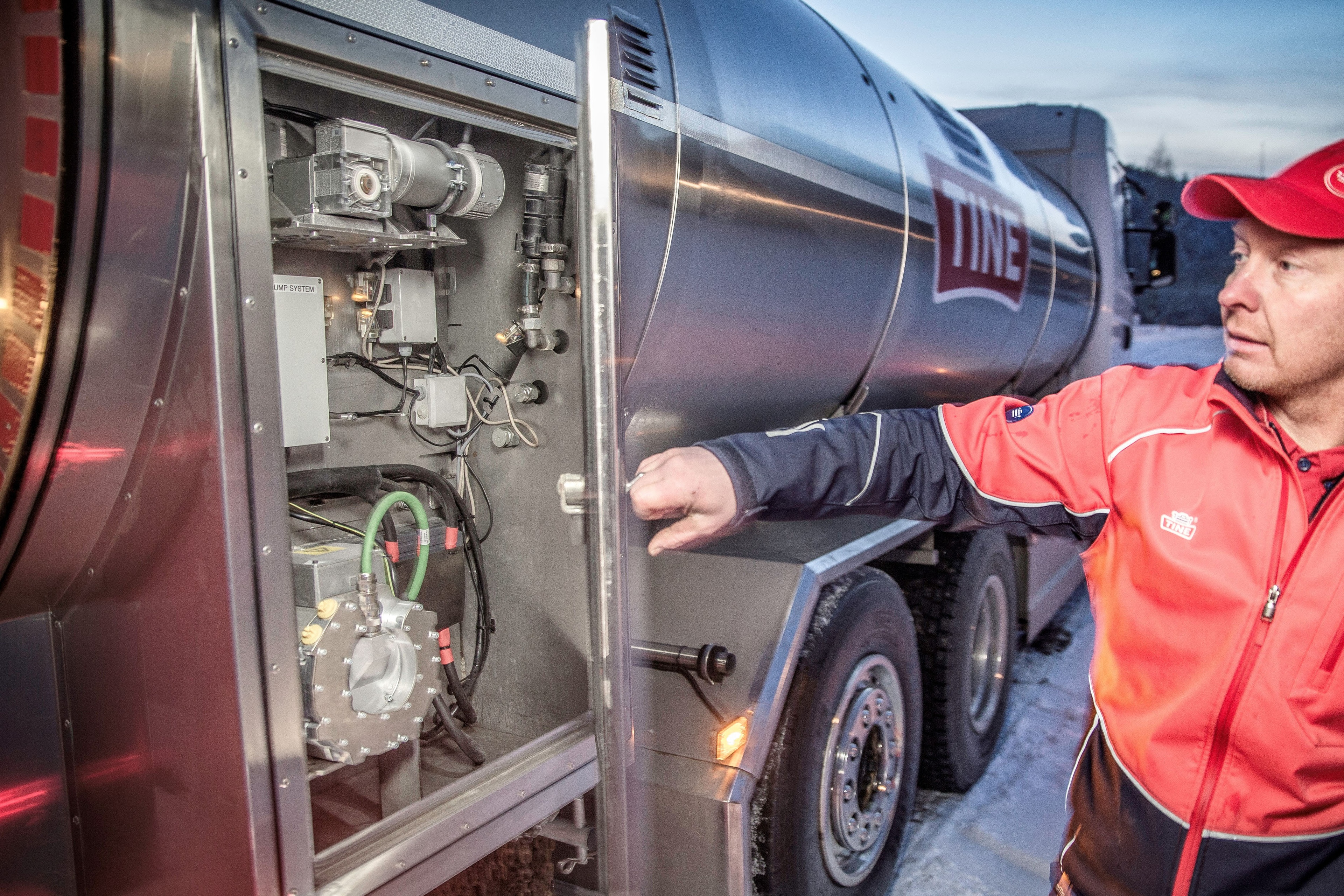
How the electric motor works
The battery for the electric motor is charged while the vehicle is in motion, like an ordinary car battery. The batteries provide enough energy for defrosters, lights, windscreen wipers, etc. – elements that help to guarantee the comfort and safety of the driver. There is hardly any noise during electric pumping, which means that disruptive noise at farms can be reduced significantly while milk is being collected.