Case
Highly accurate thermal simulations for better decisions
Westermo is one of the world’s leading manufacturers of Ethernet switches, routers and converters. In order to streamline product development, the company engaged Semcon’s simulation experts. The goal was to use thermal simulations to drastically reduce the volume of measurements of physical products and thus save both time and money.
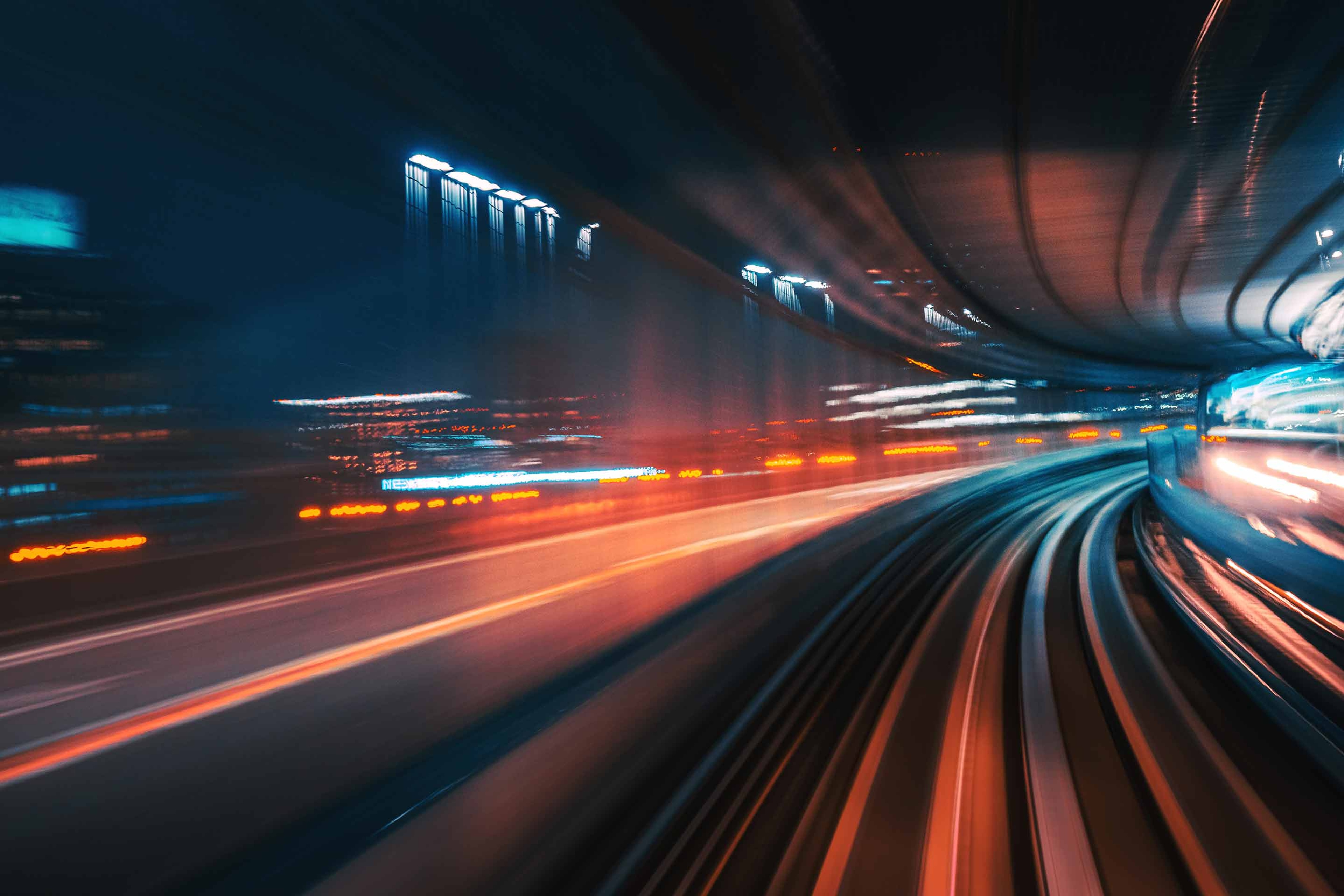
CustomerWestermo
IndustryIndustry
CompetencesSimulation & Analysis (CAE)
Background
The majority of Westermo’s products are manufactured in Sweden, but the company operates across the globe and specialises in industrial network solutions in areas such as the rail, transport and energy sectors. The environments in which the products operate are demanding, yet customers also expect long service lives. One crucial factor is how the heat that the products emit is handled in order to keep the temperature to an acceptable level.
Semcon are pros at this, and we have let them take a driving role in the project.
- Kai Lahtinen-Idö, Westermo
Avoiding costly mistakes
Demands on these types of products are increasing, while the products also need to stay the same size. This leads to more and more heat being generated, which places greater demands on the cooling of the products. There is otherwise a risk that the heat could affect the functionality, safety and service life of the products.
Westermo had previously developed prototypes for measuring temperatures and heat flows, instead of simulating. This is a time-consuming and costly process, which prompted the company to contact Semcon to investigate the possibilities of simulation-driven development.
Challenging demands on the products
Thermal simulations provide a lot of information about a product at an early stage. The initial costs are higher, but because only digital prototypes are needed, many different concepts can be tested early, and costly mistakes can be avoided.
‘So far, we’ve been working with Westermo’s switches’ says Felix Larsson, Senior Calculation Engineer, Semcon. ‘It’s important that they don’t become too hot, which is a challenge because the stringent requirements state that they have to be almost completely airtight in order to cope with a wide range of environments. The requirements also state that they cannot be dependent on cooling by fans, which means that production relies entirely on natural convection around the outside of the product.’
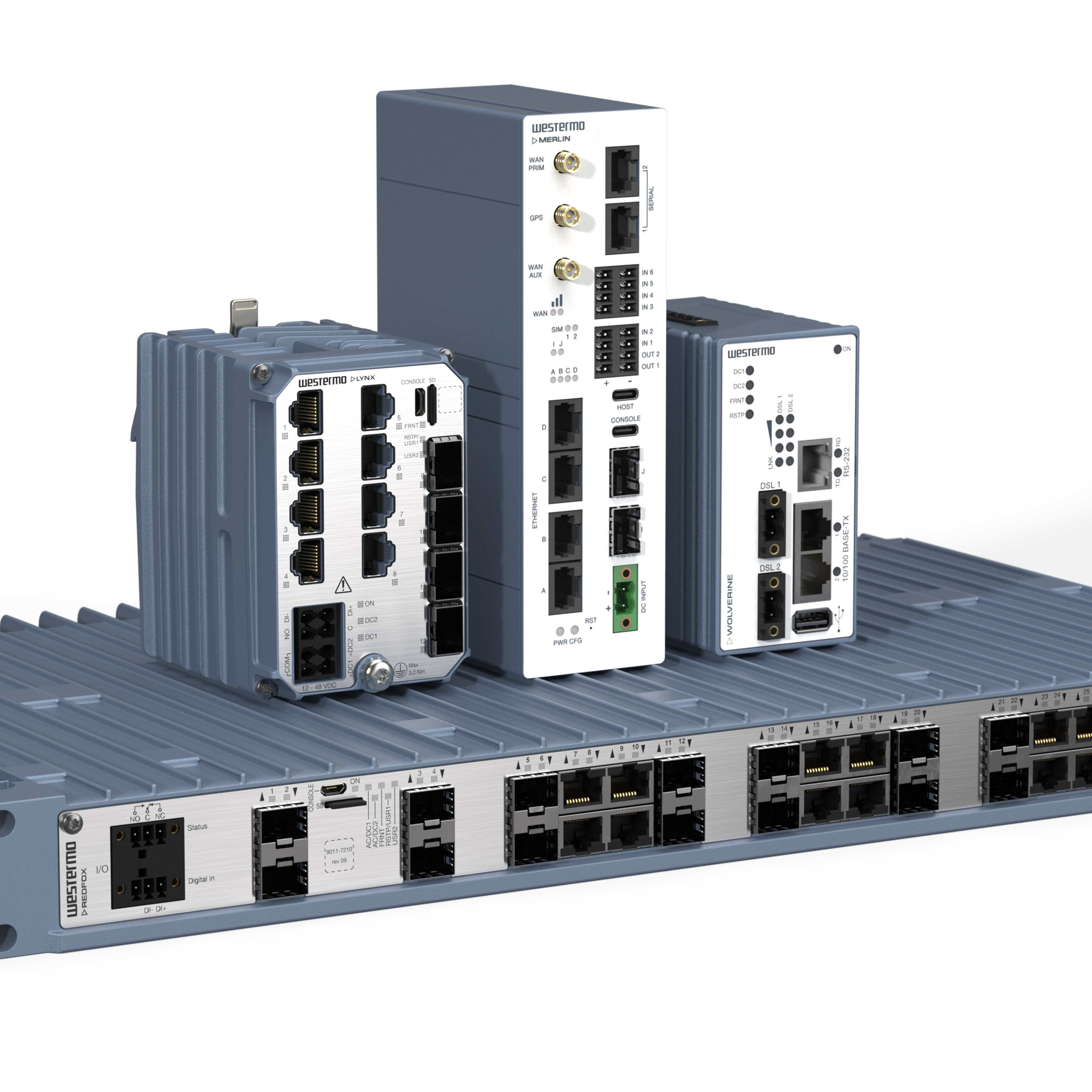
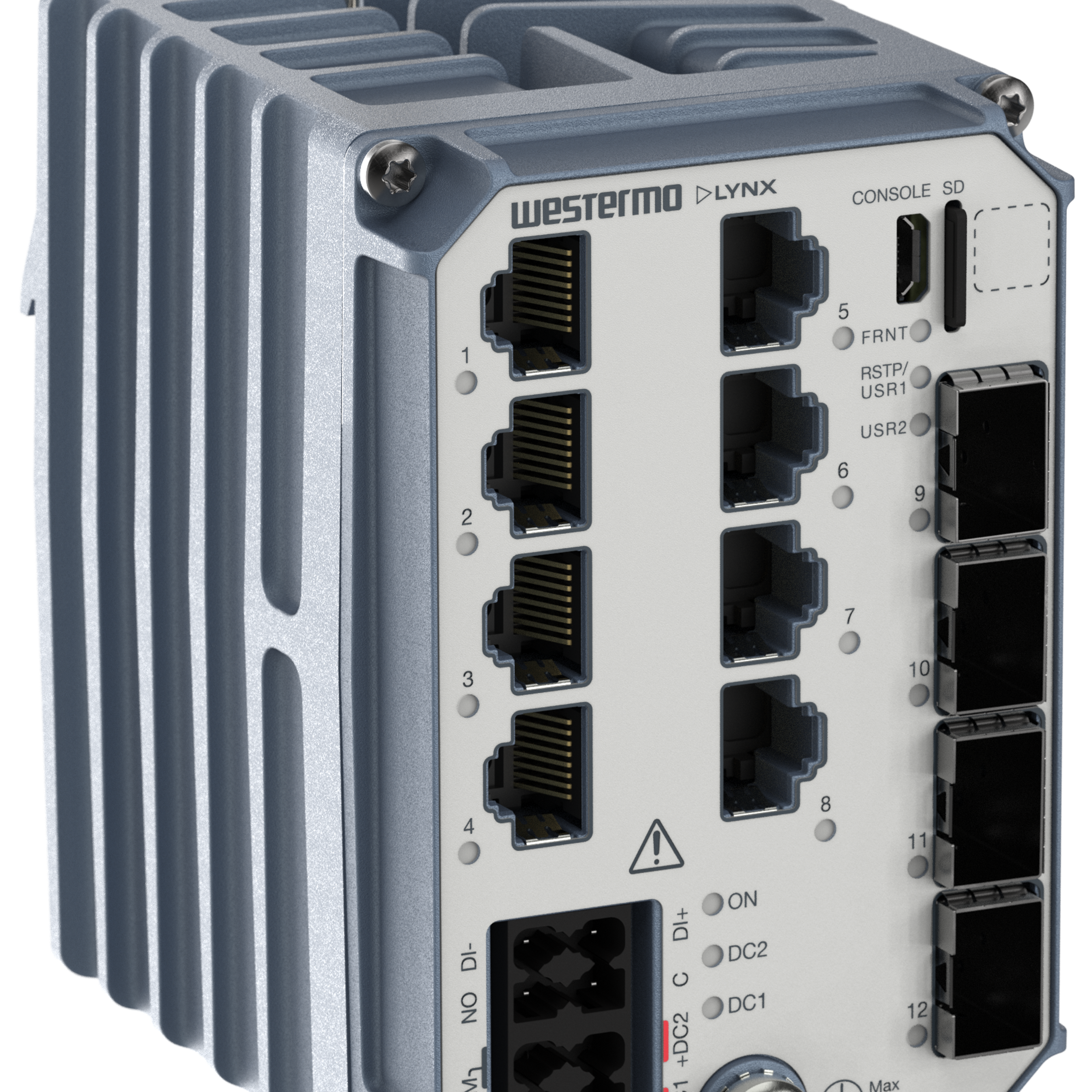
Accurate simulations led to more cooperation
In the pilot project, Semcon only received digital data on an existing product that Westermo had already begun producing. The company had conducted extensive temperature testing on the product themselves, but because they wanted to compare Semcon’s simulations with their physical tests, Semcon was not permitted to access the test results.
We had a really great collaboration, and the results of the simulation were very close to our actual results.
- Kai Lahtinen-Idö, Team Leader, Electronic Enclosures, Research & Development, Westermo
The success of the pilot project led to a new project linked to a product under development. In addition to the accuracy of Semcon’s simulations, Lahtinen-Idö also highlights the cooperation with the team at Semcon as yet another reason behind this decision.
‘The cooperation has worked really well,’ says Lahtinen-Idö. ‘We spoke the same language and had a rewarding interaction process with regular debriefings that have allowed us to arrive at the best possible results together. We want to do as much as possible without producing physical products, because this saves time and allows us to make the right decision at an early stage.’
Semcon has contributed with:
- Knowledge on where the thermal bottleneck is and suggestions for measures to address this
- Detailed insight into the internal heat distribution and circulation, which can be used to identify problem areas and optimise the layout
- Quick answers to the question ‘How does this design change affect our results?’
- An Excel-based 1D solver for very rapid results for simple design adjustments