Case
Digitalisation reduces energy consumption for Boliden’s zinc production
At the end of the Norwegian Sørfjord lies Boliden Odda. This zinc smelter has produced zinc since 1924 and today its annual production is 200 kilotons. In conjunction with the goal to increase production to 350 kilotons in the project GZO (Green zink Odda) 4.0, Boliden is determined to optimise their energy consumption and production processes. Semcon has been brought in as a strategic partner with the aim of utilising every kWh as efficiently as possible via digitalisation.
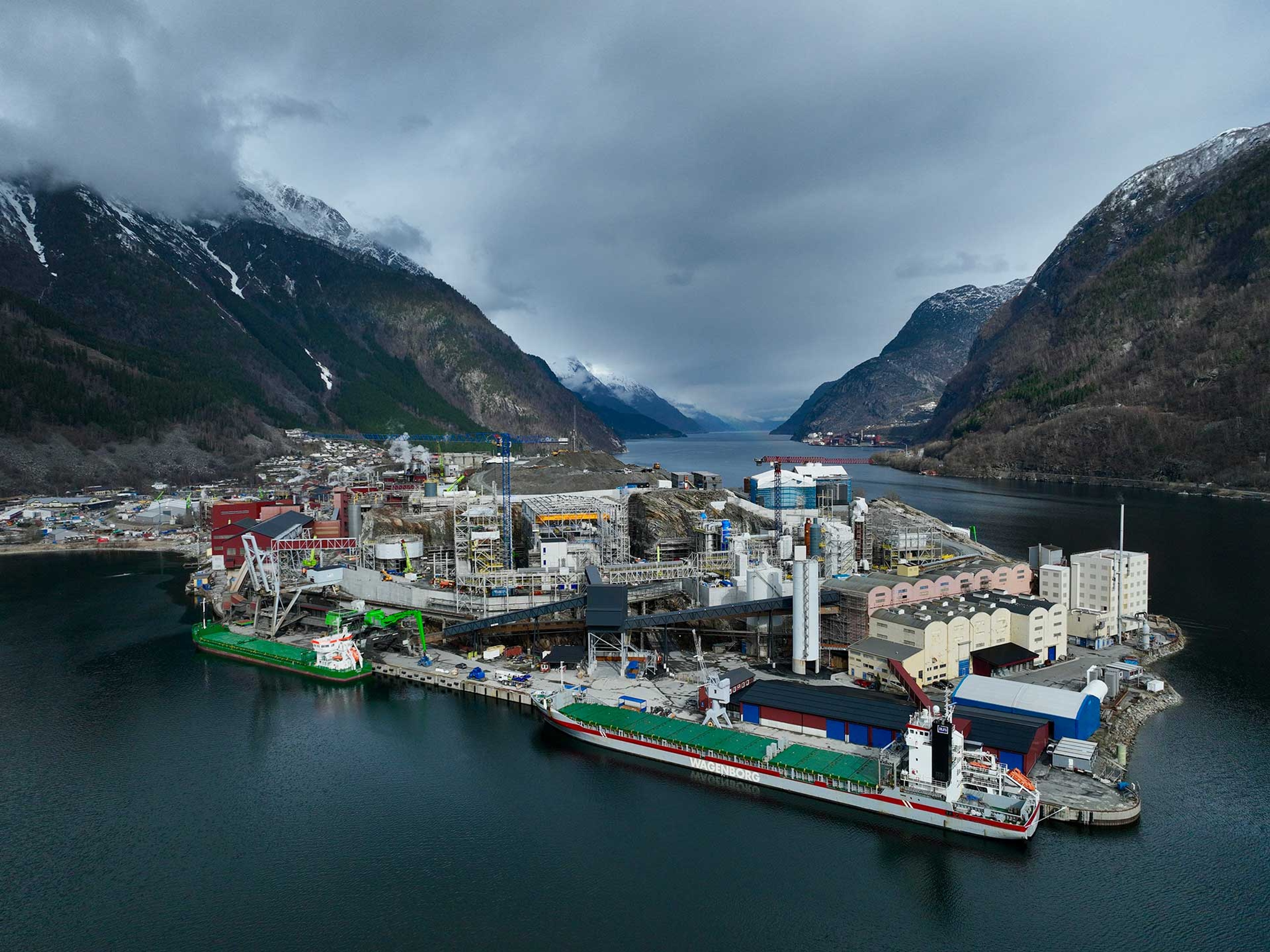
CustomerBoliden
IndustryIndustry
CompetencesStrategic Business DesignEnergy optimisationAutonomous SolutionsData Management & AIProduct Development
Background
In addition to being vital to life, zinc is indispensable to several industries. It is used, among other things, for rust protection in steel alloys and as a construction material. Zinc can be successfully recycled, a process that also takes place at Boliden Odda. However, zinc refinement is very energy intensive, and Odda itself accounts for 1% of all of Norway's energy consumption. “Even though Odda's electricity comes from local and green hydropower, Boliden intends to reduce its energy consumption as much as possible. It becomes increasingly important for the society to economize on the energy we have and of course it is also an economic issue for Boliden”, says Heidi Berg Sand, Project Manager at Semcon.
Challenge
After the Odda 4.0 expansion was decided, Boliden asked Semcon for assistance to explore the introduction of autonomous vehicles at the smelter. To select the right technology, Semcon needed to first inspect the production process in detail.
“We looked at everything from the anode plates that go into the zinc production to the production itself, storage, and transport. A lot of work went in to understanding the process to investigate where the most repetitive transportation tasks are. They can usually be optimised with autonomous processes”, says Heidi Berg Sand.
Semcon’s own workshop for testing
The Semcon team has benefited immensely from having its own workshop where there are lots of machines and prototypes that have been used for tests and in-depth knowledge of what today’s technology can accomplish.
“Semcon has looked at many different technologies and focused mainly on testing them in connection to zinc production. Can the technology cope with outdoor environments? Does communication work in the electrolysis hall and is the technology robust enough? These are examples of the issues that we want Semcon to be responsible for”, says Stein Olav Ness, Digitalisation Engineer at Green Zinc Odda 4.0.
Semcon has looked at many different technologies and focused mainly on testing them in connection to zinc production.
Solution
The project soon evolved to include strategic support in the procurement and implementation of an energy management system. Using energy mapping from Norsk Energi as a tool, Semcon has collected data and created a dashboard for Odda's energy consumption. Several parameters linked to energy are displayed in real time, which enables Boliden employees to make data-driven decisions. “Semcon works in a very structured way. They take responsibility for driving the digitalisation process forward, having a good dialogue with stakeholders, and obtaining all the information they need. They then deliver a well-substantiated recommendation to us. It is high quality and a way of working that I expect from a strategic partner”, says Stein Olav Ness.
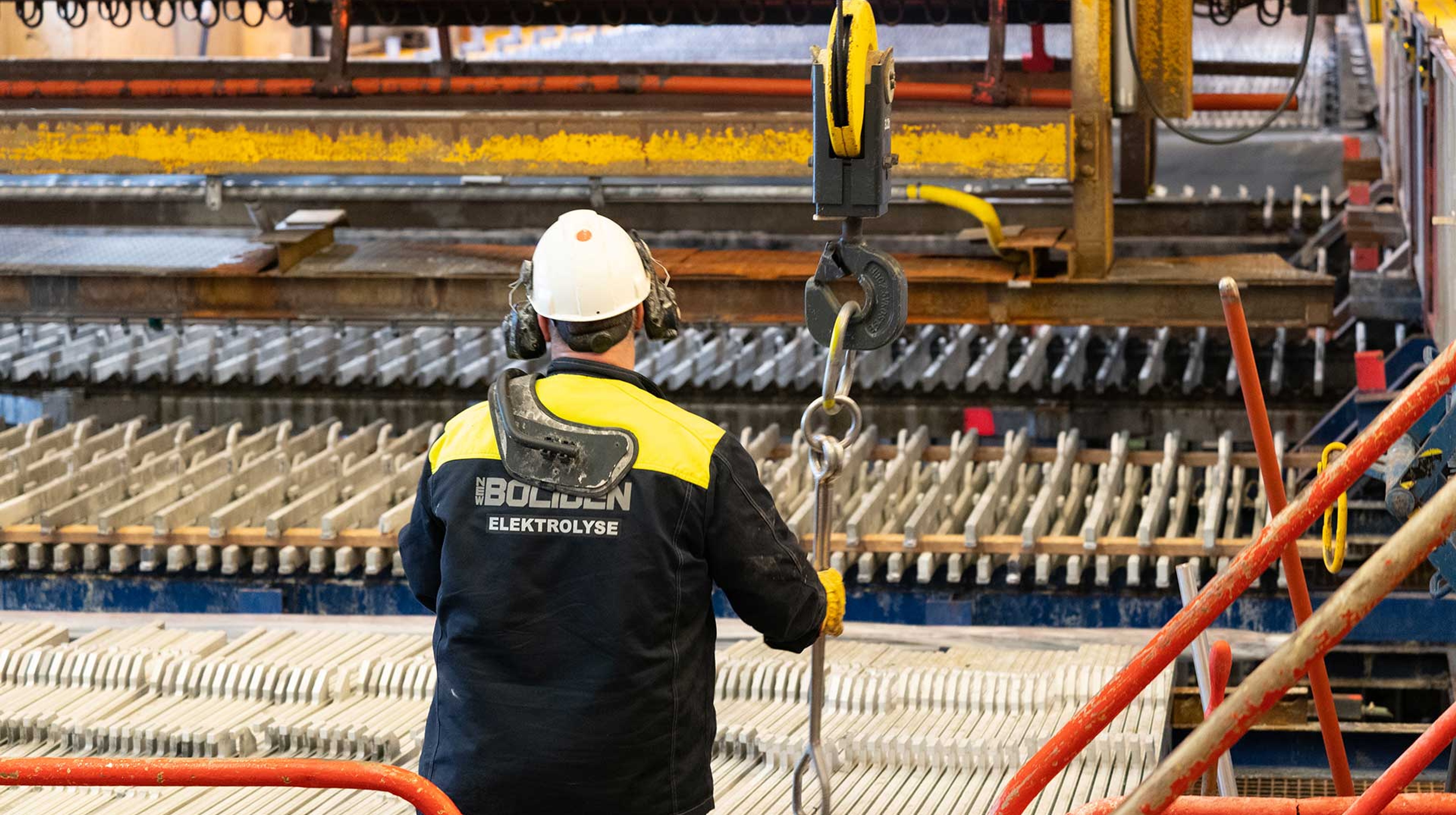
Semcon's work also includes developing use cases for various processes at Odda. This involves, for instance, compressed air, which requires electricity to produce. The new system gives each department an overview of its energy consumption for each process that requires this resource. The overall goal is to get more information and that it is available all the time. This in turn translates to better knowledge, more proactive production, and ultimately improved economics.
Semcon has contributed with:
Advisory services regarding market research and procurement of both autonomous solutions and energy management system
Implementation of energy management system
Expertise in autonomous solutions
Real-time testing and prototype development
Developing use cases to take advantage of Boliden’s newly acquired data management system
Support with change management
Expertise in digitalisation